Maintenance and Repair of Flaking Machine
The flaking machine is a mechanical device designed to increase the superficial area of particle material and destroy the cell wall of raw material, ultimately resulting in improved oil yield rates during pressing. As a key piece of equipment in oil mill plants, the flaking machine is a costly investment that requires careful maintenance to ensure a prolonged service life. Due to its high price, heavy body, and expensive repair costs, proper upkeep of the flaking machine is crucial in increasing efficiency and reducing overall production costs. Therefore, it is imperative that operators handle this equipment with care and attention to detail to maximize its performance and longevity.
1, After long-term operation of the flaking machine, both sides of the roller surface would wear seriously, which affects the effect of flaking. Thus, the two sides of the roller should be ground with a grinding wheel or other ways every week.
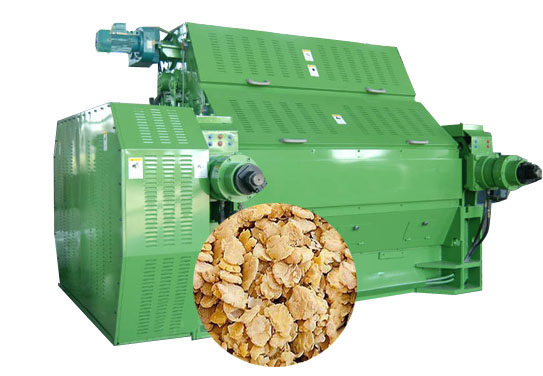
2, If impurities in raw materials are not removed completely, stones, small iron or other impurities may get into the flaking machine, thus leading to pitting on the surface of the roller so that there would be pits on the smooth roller surface. Materials after flaking have uneven thickness, which would affect the oil extraction. Then, the roller should be replaced and make the roller with pits flat. The area and hardness of roller increases, thus the turning processing is more difficult.
3, Sometime, hard feeding or less feeding of flaking machine would appear, which would seriously affect the efficiency of flaking machine. Serious vibration of flaking machine is an important cause of hard feeding of roller. The quivering roller would produce an upward force constantly to the oil plants and makes the oil plants throw up and down between two rollers. If hard feeding of roller occurs, the operator should find out the reason. Digging pit on smooth roll surface artificially to increase the friction is forbidden.
4, Broken shaft and roller edge drop. In order to ensure the quality of flaking, when the unflatness of the roller increases, the spring pressure should be increased gradually to produce a radial force on the bearing. Once the material flow is not uniform, especially there are iron, stone or other hard objects, it would lead to collision of the two rollers and the instantaneous impact is considerable. Many times of impact would exceed the axial fatigue limit and lead to the broken or edge-dropping of the shaft. It should be emphasized that the spring used to adjust the rolling distance can not be too tight. Don’t make the iron into the roller and the material flow should be uniform and don’t break, etc. These are the effective measures to prevent such accidents.
Only strengthen the daily maintenance of equipment, prevent and reduce the abnormal wear and sudden failure, the utilization rate of oil mill equipment can be improved to realize win-win situation of efficiency and effectiveness of enterprises.